Mines generate a lot of waste: waste rock known as overburden, and tailings from the processing and leaching of crushed rocks with chemicals. Extracting the valuable minerals thus leaves behind an unwelcome residue, which conventionally is dealt with in tailings ponds. This problem is particularly pronounced for bitumen mining in Alberta, where the vast scale of the production poses significant environmental problems. Tailings from other mining activities are becoming more of a problem as well. Advances in technology make it possible to exploit lower grade ores, which generates more tailings.
Tailings from bitumen mining are a mixture of water, sand, and fine clay, and also contain residual bitumen. These tailings are drained into settling ponds where sedimentation separates the ingredients. Water rises to the top, while heavier materials such as metals and minerals settle at the bottom of the pond. The difficulty arises with a middle layer of ‘mature fine tailings’ (MFT), which take a very long time to settle, even decades. This makes tailings ponds inefficient for treating tailings. Speeding up the process has become a new challenge for oil companies, which are under a mandate from Alberta's provincial government to meet capture targets for fine tailings. Introduced in 2009 as Directive 74 by the Alberta Energy Regulator (AER), companies are required to capture more than 50% of fines (particles of 44 micrometers or less) since 2013. Companies are scrambling to meet this target. In 2013, oil-sands mines owned by Shell, Suncor, and Syncrude failed to meet targets. However, the AER waived penalties.
The most common design of a tailings pond is the raised embankment. The initial embankment (the starter dyke) is raised from time to time to accommodate the growing layers of sediment at the bottom of the lake. An improvement involves thickening the tailings by dewatering them mechanically through compression and filter presses—a technique used at the Kidd Creek copper and zinc mine near Timmins, Ontario. However, it took many years before this technology became practical due to inconsistent thickening. Advantageously, with this technique reclamation costs are significantly lower than with conventional ponds. They are also safer with respect to the potential instability of high retaining embankments of conventional ponds. The third option involves ‘dry stacking’, dewatering the tailings into a ‘cake’ that needs to be transported by conveyor belt or truck rather than pipeline. Dry stacking employs different types of drying and filtering. One method uses stacked pressure plates and vacuum filtration systems. Other methods involve centrifuges or thermal drying in kilns. Dry stacking is very advantageous environmentally. It recovers water that can be reused for processing ore. It eliminates the risk of catastrophic dyke failure, especially in seismically-active locations. It is possible to reclaim and rehabilitate land progressively instead of after mine closure. It also works well in cold climates, where pipe freezes and frosting can impede the operation of a tailings pond. Lastly, groundwater contamination through seepage is virtually eliminated. Of course, these numerous advantages come at a cost. Filtering and drying takes energy, which can add considerable expenses. Unfortunately, dewatering tailings rich in bitumen is difficult without adding more chemical reagents, which makes this process even more costly.
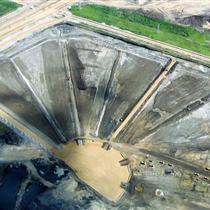
There are solutions that may close the gap between environmental ambition and economic reality. Suncor employs a novel method known as ‘consolidated tailings’, which involves mixing a polymer flocculant into the MFT and depositing the mixture in thin layers over sand banks with shallow slopes. This results in relatively dry material that can be reclaimed in place or transported to other locations. The advantage is that the process only takes weeks rather than years. Advantageously, the process can also be applied to drain and process MFTs from existing conventional tailing ponds. Shell uses a similar approach, but calls it ‘atmospheric fines drying’. It is pictured above, at Shell's Muskeg River mine. Engineers refer to this entire class of methods as ‘chemical amendment’—adding flocculants.
‘It is time for Alberta's regulator to grow sharper teeth.’
As the discussion above suggests, the trouble with tailings ponds is both technology and economics. New technologies need to be developed and tested as some may work better in some environments than others, and the most effective technologies to date increase costs, primarily due to the energy involved in drying. Companies need to be prepared to bear the full cost of clean-up, and invest more into R&D for dealing with tailings. Alberta has been lax about enforcing its own environmental targets. Penalties were waived and variances (lower targets on a case-by-case basis) were granted. It is time for Alberta's regulator to grow sharper teeth. The industry complains that the methods stipulated in Directive 74 put them into a technological straight-jacket. While there may be a need for more flexibility in technological approaches, flexibility should not be confused with laxity. If oil companies want to expand oil sands exploration in Alberta, they should set themselves more aggressive goals for reducing their environmental footprint.
Technical notes: Flocculants are chemicals that remove suspended solids from liquids through a process of contact and adhesion whereby the particles of a dispersion form lager-size clusters. Common flocculants are polyacrylamides, long-chain polymers. Coagulation is synonymous to flocculation. Further information can be found in the report Oil Sands Tailings Technology Review prepared by BGC Engineering, July 2010.
![[print]](print.png)
![[Sauder School of Business]](logo-ubc-sauder-2016.png)
![[The University of British Columbia]](logo-ubc-2016.png)