The international market for liquefied natural gas (LNG)
would not exist without the ability to carry it from port to port
over great distances while keeping the product cooled below
–162°C. The idea of liquefaction goes back to
German engineer Carl von Linde who built the first practical
liquefaction equipment in 1873. The first LNG plant was built
in the United States and went into service in 1917, but commercialization
did not start until decades later.
The first LNG tanker, the Methane Pioneer, was commissioned in 1959,
and in 1964 the age of international LNG began with shipments
from Algeria to the United Kingdom.
LNG tankers must be able to withstand the extreme cold temperatures of the liquefied gas and prevent the hull from cooling and becoming brittle. At the same time, the tanks must insulate the LNG from gaining temperature. The design must also prevent mixing of gas vapor with air. Two designs have emerged that facilitate this. The most common type is the self-supporting spherical tank, known as the Moss design. LNG is stored in spherical aluminum tanks, where the top half protrudes above the deck.
The membrane design is a newer development where the tanks are below deck and are fitted into the hull. A primary membrane made out of steel or a nickel-iron (Invar) alloy encloses the LNG. Invar steel has desirable properties: it expands or contracts very little with temperature changes. An insulating layer of polyurethane foam or perlite separates the primary membrane from the secondary membrane, which provides additional protection and back-up if the primary membrane leaks. A second foam layer separates the tank from the hull of the ship. Membrane tanks are box-shaped rather than spherical.
‘The LNG tanker fleet has expanded hugely in recent years.’
As the chart below shows, the LNG tanker fleet has expanded hugely in recent years. There are now about 400 LNG tanker ships in service and more are under construction. Many LNG tankers are only a few years old, and many of them have been built in South Korea (Daewoo, Samsung, and Hyundai) and Japan (Mitsubishi, Kawasaki, and Mitsui). A new tanker costs around $150-175 million, with some of the larger exceeding $200 million. Once commissioned, most ships are dedicated to service a particular route and a particular long-term (usually 20-year) contractual relationship. A few ships have been built to service short-term LNG needs.
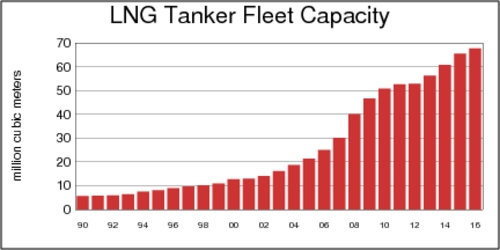
LNG tankers are becoming larger and more efficient. The membrane design makes better use of available space on a ship and thus facilitates lighter hulls. Conventional LNG ships in service today are often in the 138-145,000 cubic meter range. The Q-Flex class of ships in service since 2007 reaches 210,000 m3, and the Q-Max class even 260,000 m3 since 2007. The "Q" in the name refers to the ability to dock at Qatar's LNG terminals. These large LNG tankers are dedicated to very specific routes because most LNG terminals cannot handle such large ships.
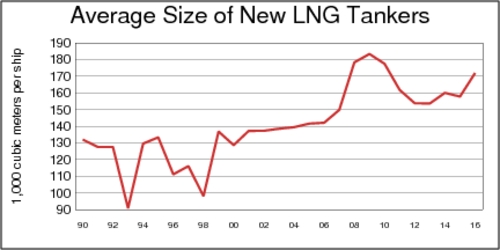
The chart above shows the average size of tankers put into service since 1990. The average in the 1990s hovered around 130-140,000 m3, with a few dips. The years 2007-2009 saw the emergence of the Q-Flex and Q-Max class of ships with membrane designs. However, the average size has dropped back to about 150-160,000 m3 in the last few years because much of the recent additional demand in LNG comes from Japan, the world's largest LNG importer today. Existing terminals in the Tokyo Bay area restrict the maximum size of LNG tankers.
It is also interesting to note the propulsion system of
LNG tankers, which is based on steam turbines in most instances.
Many tankers use a dual fuel egine that can
burn both conventional bunker fuel (heavy fuel oil, or HFO)
as well as natural boil-off gas (BOG) from the LNG tanks.
Some designs also allow forced boil-off gas to be used, when
fuel demand is higher than is available through natural
boil-off, and when LNG is cheaper as a fuel than HFO.
Newer designs also employ dual-fuel
electric propulsion, which tends to reduce emissions further
and provide greater efficiency (albeit at greater capital cost).
Electric propulsion is also more compact because the generator
and propellers no longer need to be connected through a rigid shaft,
thus leaving more space for cargo. One such ship is the
British Emerald (pictured on the right), a double-hull vessel
equipped with dual-fuel diesel-electric engines, operated
by BP Shipping and built by Hyundai in 2007 for $185 million.
This ship employs the membrane design with four separate tanks
and can carry 155,000 cubic meters of LNG.
Ships are not only used for transportation, however. South Korea's Samsung Heavy Industries is building the Prelude, the world's first ocean-based LNG plant for Royal Dutch Shell. The hull was launched in late 2013. This floating LNG plant will cost over $12 billion and is due to be completed in 2017. Once operational, it will be servicing offshore LNG gas fields, off Autralia's north-west coast. With a displacement of 600,000 metric tons of water, the Prelude will be the largest ship on the seas. A spectacular synthetic picture provides a fascinating view of the construction of this vessel.
- Stephen Mallon: The Biggest Ship in The World (Though It Isn't Exactly a Ship), The New York Times Magazine, October 31, 2014.
- World LNG Trade Database: Shipping Fleets
- World Fleet of LNG Carriers (Feb. 2012) from Auke Visser
- LNG Carriers in Service or Under Construction (Sep. 2013) from Tim Colton
![[print]](print.png)
![[Sauder School of Business]](logo-ubc-sauder-2016.png)
![[The University of British Columbia]](logo-ubc-2016.png)