Since the outbreak of the SARS-CoV-2 virus and the resulting COVID-19 disease, governments and businesses around the world have found themselves in unique and unprecedented economic circumstances. In a world of global supply chains supported by international trade, disruptions in one place can quickly ripple through the global supply chain and cause disruptions elsewhere. A question that I am often asked these days if the experience today will have lasting repercussions on how global supply chains are organized in our post-COVID-19 future. The answer is—you probably guessed it—not a simple yes, because there is a fundamental trade-off involved. Let me explain why more resilience is needed but difficult to accomplish.
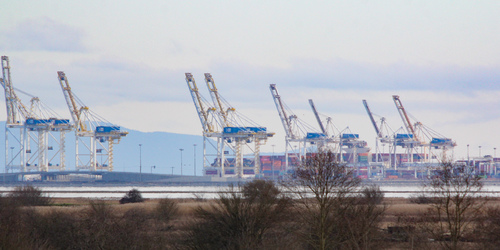
Why are global supply chains fragile?
‘Global supply chains are vulnerable due to their leanness and complexity.’
There are two aspects to this question: leanness and complexity. Modern businesses have adopted lean manufacturing that keeps inventory levels low and supplies parts and components in as near real-time as possible. This means that the flow of parts needs to be highly reliable and without delays. That in turn allows firms to minimize their inventory and avoid the cost of holding such inventories (and providing storage capacity for them). The downside is that the occurrence of unexpected disruptions in the supply of parts leads to output curtailments. This is the supply-side inventory optimization problem. (There is also a demand-side inventory optimization problem for produced output, due to oscillations of incoming orders.) Now enter the second problem: complexity. Many technological goods are made up of many separate components. Have a look at Apple's iPhone in the visualization shown in an article by Dennis Wong in the South China Morning Post from 2016: Anatomy of an iPhone: what's in it and where the parts come from. Components come from the US, China, Taiwan, South Korea, Germany, Japan, Britain, and the Netherlands. They are assembled in China and shipped to consumers worldwide. What happens if something happens to one of these 34 suppliers? As soon as the assembly plant is out of inventory, the production line comes to a halt. The more complex the product, the higher the risk of a disruption. I refer to this problem as complexity risk. Idiosyncratic risk at one supplier is magnified and become systemic risk to the supply chain. To counter it, businesses need a degree of supply chain resilience.
What is supply chain resilience?
‘Resilient supply chains exhibit redundancy, flexibility, and empowerment.’
Supply chain resilience is the ability of a network of supplier and manufacturers to respond to adverse events and either return quickly to the normal state or adapt quickly to a permanently altered state. This, first of all, requires an assessment about whether the final state is going to be "business as usual" or "business has changed forever". Is the disruption temporary or permanent? Naturally, different sources of disruption may require different adaptation strategies. What do these strategies have in common? Supply chain resilience has three main ingredients: redundancy, flexibility, and empowerment.
Redundancy is the easiest concept to grasp, but also the most expensive to execute. It require businesses to keep larger inventories and spare capacity (or equivalently, operate with lower capacity utilization). There is a significant cost to that as spare capacity and increased inventory both require capital. The trade-off here is clear: resilience comes at the expense of efficiency. Too much redundancy will give competitors an edge in "normal" times. We therefore need to define a "safe standard" for managing inventory and capacity. There is yet another way to achieve redundancy by sourcing identical goods from different suppliers. This "hedging" approach works great if you have multiple suppliers that can provide goods of similar quality and cost. However, this often does not work well when there is a monopoly supplier, or one with unique expertise or unique economies of scale. Redundancy has obvious limitations.
Next is flexibility. Supply chains are all about procurement and making sure that parts and components are not only cheap, but also "fit". In a world of complex technological goods, we rely on a high degree of standardization and compatibility. Thus, businesses benefit when then rely on generic parts (providing compatibility) and standardized procurement processes (that enable quick switching among competing suppliers). A flexible business is also one that can handle procurement processes concurrently rather than sequentially. When adverse situations strike, it is unlikely that they affect only one part of the operation. It is more likely that multiple supply lines need to be rejigged at the same time.
Postponement planning is another flexibility tool. Using a stock for semi-finished goods rather than inventories of raw supplies allows for maintaining constant output for longer. Consider a product that requires components A, B, C, and D in that sequence. If we hold some semi-finished product made of A+B, we can complete the product later with components C and D. If supply link A or B goes missing for a while, we can simply switch to the semi-finished goods A+B waiting for completion. Temporary failure of supplies for A or B thus give us more time to adjust.
The nature of the supplier relationship matters as well. Procurement strategies need to be aligned with the supplier. This means closer integration and making relationship-specific investments. In order to have credible alternatives, it is necessary to explore compatibility of alternative parts and components in order to be ready to switch to an alternate supplier when the need arises. A firm needs to understand the capabilities of their actual and potential suppliers alike in order to ensure that parts and components are compatible. Standardization (so that things are compatible) is key to ensuring flexibility.
Supply chain flexibility may also be needed when firms are forced to change their production lines. This means demand for particular components may quickly change. How much flexibility is built into the contracts to adapt to changing needs? Can order sizes be quickly changed, and will the supplier have the capacity to fill increased orders? How easy it is to back out of all or part of an existing order without invoking force majeure? The current COVID-19 crisis has prompted some firms to switch production from auto parts to ventilators, and from perfumes to hand sanitizers. Flexibility in a business requires knowing your own ability to adapt quickly to changing market needs and also the ability of your supply chain to respond to changed needs.
Flexibility also has a geographic aspect. The universal truth about risk management is that idiosyncratic risk can be diversified, but not systemic risk. A worldwide pandemic hits, that is systemic risk if it hits everywhere. But it may hit at different times in different places. That is idiosyncratic risk. We can diversify that risk geographically by not relying on one manufacture in one place alone. Unfortunately, there is a huge caveat: the alternative sources may be in higher-cost locations. When the going gets tough, cost is often not the first concern. When supply is curtailed, prices go up. That gives room for sourcing supplies from another higher-cost supplier if needed. However, in order to be able to do so we need the compatibility alluded to earlier; we need standardization to ensure compatibility.
The link between supplier and producer is transportation. If disruptions affect transportation providers (as they often do due to weather and other conditions), how can goods be routed alternatively? Long distance is a problem and often impedes lean manufacturing and just-in-time delivery. Many suppliers, especially in the auto industry, thus produce in close proximity to their main customers. This minimizes transportation risk.
Lastly, there is empowerment. This is the most misunderstood concept among the three principles of resilience. It requires a cultural change within the corporation: the ability to anticipate and prepare for worst case scenarios. This culture of fail-safe thinking is prevalent in some industries that deal with technical risk and high risk of injury to workers. Fail-safe thinking is, simply put, plan for the worst but always hope for the best. It is no mistake when NASA puts triple redundancy in spacecraft; there is often only a single chance to "get it right". Fail-safe thinking involves allowing for high-impact low-probability (HILP) events rather than the more common low-impact high-probability (LIHP) events. Think about it as earthquake risk. Small tremors are common, but the "big one" only occurs every few hundred years. But when the "big one" comes, we want to be prepared as much as we can. Businesses are often like people who don't own earthquake 72-hour survival kits. It's painful to think about adverse outcomes, so we stick our heads in the sand rather than acknowledge the possibility of adversity.
Empowerment is the institutional counterpart to fail-safe thinking. Remember the space shuttle disaster in 1986 when Challenger broke apart 73 seconds into its flight and killed all seven crew members? It turned out that an O-ring seal had failed in one of the booster, but concerns raised by engineers beforehand were routinely ignored and sidelined. Key information never reached the top of the administration and was systematically stymied at mid-level. Empowerment is necessary to cut through the chain of command when the problems in a business could become existential. There needs to be a culture of open and frank internal communication to anticipate problems and deal with institutional inertia. When businesses run into adverse situation, risk management must be quick and decisive. Mid-level managers need to be ready to make decisions when decisions need to be made on the spot in order to keep the problem from getting worse. Risk management thus involves empowerment conditional on the crisis context. If a business is organized too hierarchical, some decisions are not taken in a timely manner because mid-level managers wait for decision from top-level managers. Often, mid-level managers know much better the "ground truth" of a situation because they are already dealing with it, and then need to have the power to make decisions quickly and decisively. This in turn requires a culture of training and trust. Training prepares for eventualities, and training develops trust in making sound decisions that are in line with a company's values and principles.
How much resilience is "just right"?
‘Because there is no single metric for resilience, it is difficult to know what amount is sufficient.’
Everyone is familiar with the Goldilocks Principle (named after the children's story "The Three Bears"): we prefer the outcome that is neither too cold nor too hot but just right. In analogy, we prefer the level of resilience that is just right, not too little but also not too much. So how much resilience is "just right"? The problem is that the answer is not a simple optimization problem because it involves trade-offs that are hard to quantify. So what exactly is the trade-off? On one hand is efficiency and low cost. On the other hand is output certainty. Thus the key question becomes: what is the value of output certainty? For some goods, delays do not matter much. During the current COVID-19 crisis we see that some goods are more essential than others. The new smartphone or computer can wait a few months if needed. Companies will be able to recover lost output eventually. Other companies must deliver no matter what. Medical supply chains are the most important. Resilience is paramount to ensure that we can deliver medicine to save lives.
Will COVID-19 have a lasting impact on global supply chains?
Supply chains are all about specialization and lower costs. We produce in locations that have the lowest cost comparative advantage or can offer the best economies of scale. The quest for efficiency will not simply disappear after COVID-19. There simply won't be a large-scale repatriation of business activity, or deglobalization as some have suggested. Simply put, each type of risk has its own different footprint on how it affects supply chains. This is also the reason why resilience can't be measure easily. You can only measure resilience when you know what risk you are ensuring against. If you don't know which risk, or which risk has what frequency of occurrence, it is impossible to have reliable metrics of resilience. I call this the resilience ambiguity problem. We know roughly what resilience is, but we can't measure it precisely.
‘COVID-19 will not lead to a deglobalization of supply chains; the gains from trade are much too beneficial.’
Repatriation of outsourced business activities, favoured by nativist politicians, may not even be possible in many instances. Often there are no longer any domestic supplier networks that can be tapped into, and rebuilding them would be difficult and expensive. Unless governments subsidize infrastructure for "critical production" or protect a domestic industry from foreign competition through tariffs or regulation, market forces will still gravitate towards efficient low-cost production solutions all around the world. That's the beauty of international trade, and at the same time its Achilles Heel when global misfortune strikes. Governments should be extremely reluctant to mandate resilience standards except in life-critical areas such as medicine. Reports where some countries have started hoarding medical supplies and stopped sharing supplies with neigbhours is deeply troubling. Resilience within businesses will mostly come as careful assessment of strategic alternatives: making a business less dependent on others by anticipating and allowing for possible disruptions. Put simply, always have a "plan B". The resilient business survives, while the oblivious business eventually ends in failure and bankruptcy.
COVID-19 will have some important lessons about supply chains. Businesses will start taking resilience more serious. Fail-safe thinking needs to take root deeper than in the past, supported by internal communication and management structures in a business. COVID-19 will not end globalization, nor should it. Where change is needed most is at the global industry level to deal with global systemtic risks. Cpmpanies are competitors and don't see themselves as collaborators. However, in a crisis, competitors must collaborate for the greater good of society. This type of industry-level planning for global crisis management is still wishful thinking—it is hard to accomplish even at the national level. When push comes to shove, global interests still take the backseat to national interests. Sadly, supply chain resilience in the face of a global pandemic collides with the reaility of strategic national interests.
In an insightful piece in Foreign Affairs, Henry Farrell and Abraham Newman asked Will the Coronavirus End Globalization as We Know It?. Their argument is that globalization will shift in the face of shifting geopolitics. Perhaps businesses will become more reluctant to rely on single-source (single-country) supply chains. Realizing vulnerabilities, some supply chains will be ruptured to form new, more resilient links. If the authors are right (and I tend to agree), you can expect COVID-19 to reshap geopolitics of globalization.
Further readings and information sources:
- Global Supply Chain Disruptions From Coronavirus Will Pressure China's Trade and Western Supply Chains Buckle as Coronavirus Lockdowns Spread Reuters, March 12, and March 23, 2020.
- Henry Farrell and Abraham Newman: Will the Coronavrius End Globalization as We Know It?, Foreign Affairs, March 16, 2020.
- Tom Linton and Bindiya Vakil: Coronavirus Is Proving We Need More Resilient Supply Chains, Harvard Business Review, March 5, 2020.
- US Department of Homeland Security: Supply Chain Resilience Guide, April 2019.
- Thomas Ebel, Erik Larsen, and Ketan Shaw: Strengthening health care's supply chain: A five-step plan, McKinsey & Co., September 2013.
![[print]](print.png)
![[Sauder School of Business]](logo-ubc-sauder-2016.png)
![[The University of British Columbia]](logo-ubc-2016.png)